What is a DC Generator?
A DC Generator is an Electrical Machine that converts Mechanical Energy into DC Electrical Energy. It mainly consists of the armature, and field coils which work as electromagnets in it. There are so many parts of the DC Generator which play a significant role during its working. A DC Generator works on the principle of Faraday’s laws of electromagnetic induction. It provides DC Electrical Energy which is used in many applications like DC transmission lines, heavy DC Power Supplies, etc. So, let’s discuss the working principle of a DC Generator first and then we will move on to the construction of the dc generator and will study furthermore topics and details of the dc generator below:
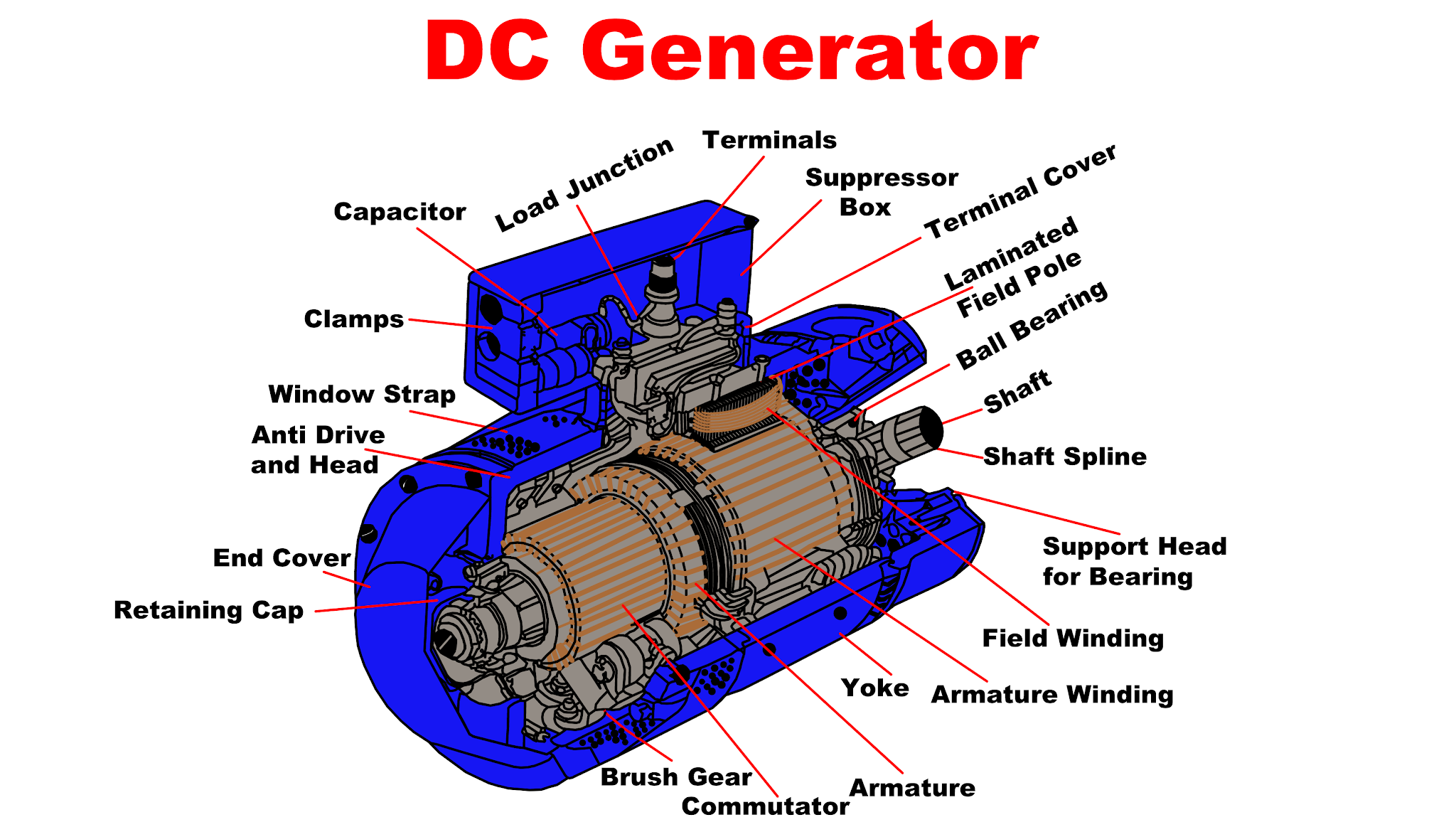
Working Principle of DC Generator
The working principle of a dc generator is same as the Faraday’s law of electromagnetic induction and a simple loop generator/ loop generator. The working principle of a DC generator is when the armature starts moving through the mechanical energy applied on its shaft then the armature coils produce an EMF. This EMF links with the field poles Due to magnetic flux and the current is generated in the field poles to provide DC on its output terminals/load terminals. For Further understanding let’s move on to Faraday’s Laws of Electromagnetic Induction below:

Faraday’s Laws of Electromagnetic Induction
Basically, faraday’s law of electromagnetic induction is further divided into two slightly different laws and the dc generator works on Faraday’s first law of electromagnetic induction. Both Faraday’s Laws of electromagnetic induction are described below:
Faraday’s First Law of Electromagnetic Induction
Faraday’s first law of electromagnetic induction states that “When a conductor cuts a magnetic flux, an EMF is induced in that conductor.” A Simple loop generator/loop generator is based on this law of electromagnetic induction.
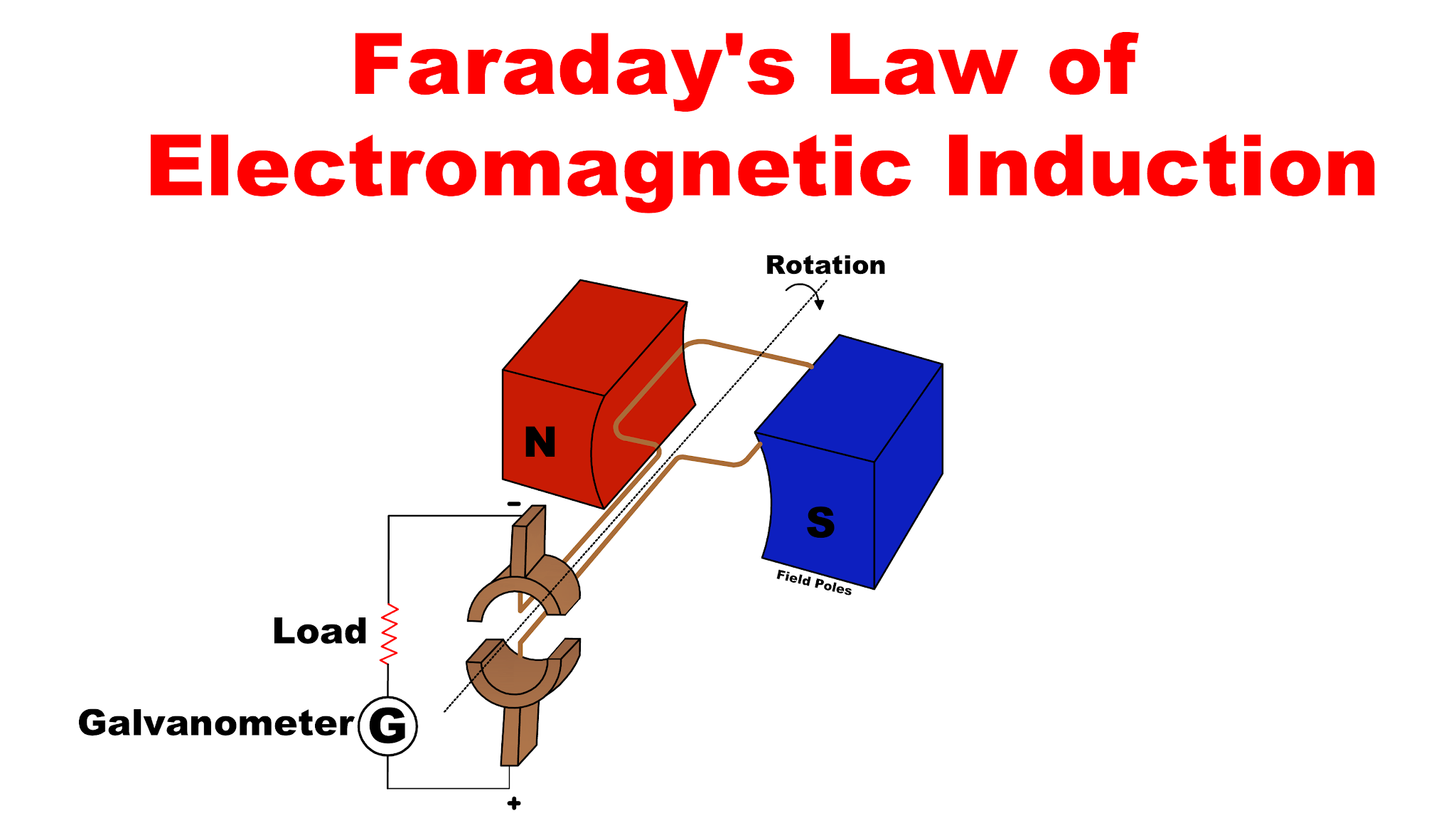
Faraday’s Second Law of Electromagnetic Induction
Faraday’s second law of electromagnetic induction states that “The magnitude of generated EMF in a conductor(wire) is equal to the rate of change of flux linkage.”
The conversion of mechanical energy into electrical energy is based on Faraday’s first law of electromagnetic induction and this law is used in the construction of a DC Generator. Without this law, the DC Generator is not capable of converting mechanical energy to DC electrical energy.
For further explanation of the Working Principle of a DC Generator, let’s move on to the Simple form of a DC Generator named a Single loop Generator. This generator works exactly on Faraday’s First Law of Electromagnetic induction. This Loop Generator is described below in further detail:
Single Loop Generator
A Loop Generator / Simple Loop Generator is a basic concept of the DC Generator. It is a conductor placed between the magnet bars. These magnetic bars may be of permanent magnet or electromagnet. The basic working of the simple loop generator is that when the two wires, conductors, or coils are placed between the magnet bars and imagine the coil is rotating clockwise, the flux starts changing its value and as a result, EMF is induced in it.
Construction
A simple loop generator basically consists of two conductors or coils; two magnet bars two slip rings(which are insulated with each other and from the central shaft) and a normal wire for connection as required. The rotating coil may be assumed as armature and the magnet bars field magnets.
Working Principle
Assume that the coil or the two conductors are rotating in a clockwise direction. The coil has a fixed position between the field and the flux linked with it starts changing its value. As a result, EMF is induced in it and it is proportional to the rate of change of flux linkage. When the coil reaches 90 degrees in the process of rotating, the coil slides don’t cut the flux, and the flux moves parallel between them. As a result, EMF is not induced in the coil. As the coil continues its rotation, the amount increases to its maximum and when the coil reaches 90 degrees then in this case maximum EMF is induced in the coil this is because the maximum flux is produced.

The result is that when the coil rotates from 90 to 180 degrees, the flux increases gradually and the rate of change of flux linkage decreases.
When the coil rotates from 180 to 360 degrees the variation occurs in the magnitude of the EMF. At first EMF remains similar in the middle position EMF reaches its maximum and at the end minimum EMF is produced.
Conclusion
Remember that the current produced in the coils is alternating and we get this current rectified by the split rings. Hence it is clear that the armature of the DC Generator also provides Alternating Voltages.
Construction of DC Generator
The construction of a DC generator mainly consists of a yoke/main cover, pole cores, field coils, armature, windings, etc. Each part of the dc generator has its own importance according to its working and function so these parts are described below in further detail and explanation:
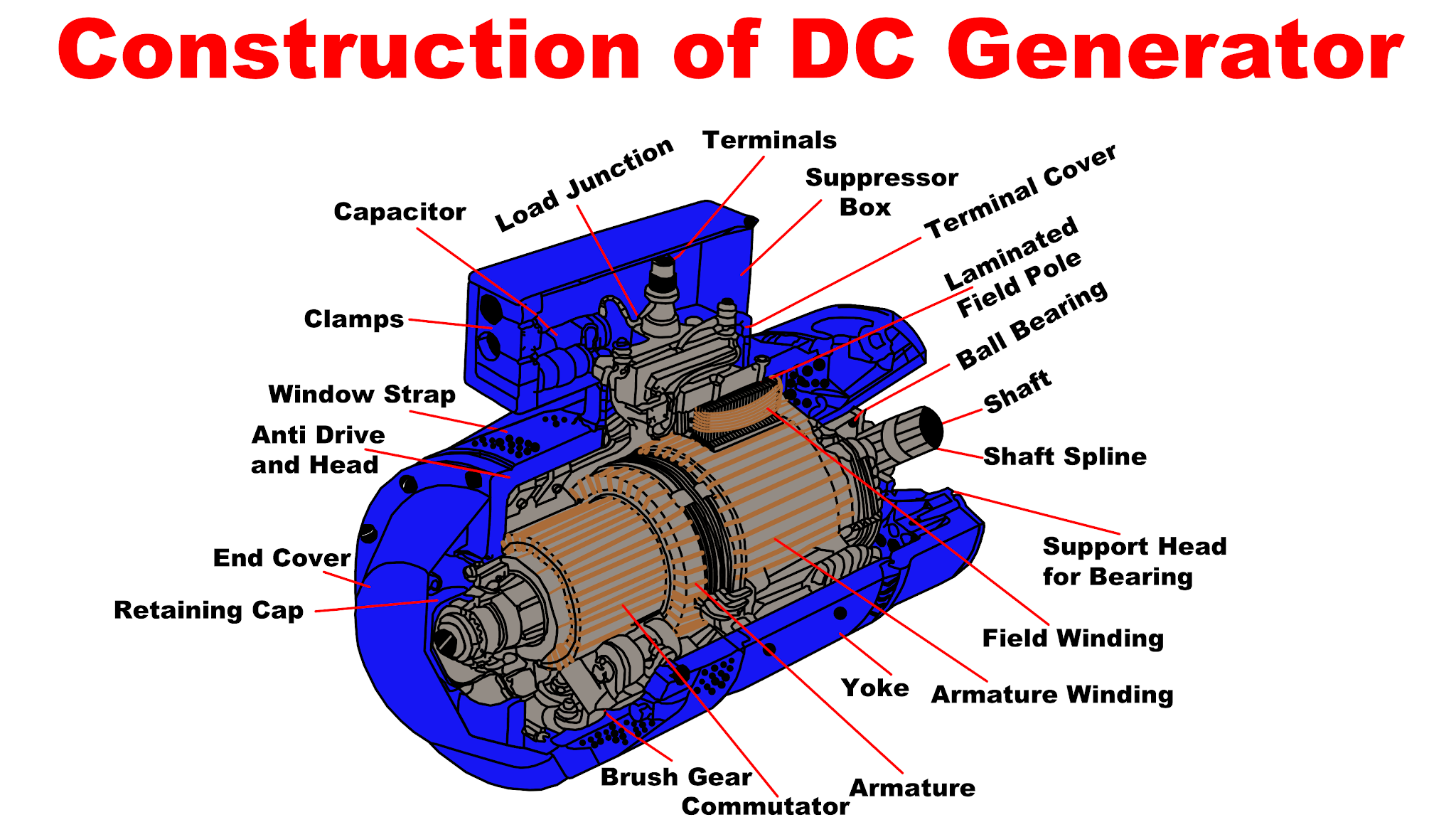
Parts of the DC Generator
DC generator consists of the following main parts:
Yoke/Main Cover: The yoke is the main cover of the DC Generator made up of iron or any other material
Pole Cores: Pole Cores are used as field magnets. These are used to spread out the flux in the air gap and it is also used to support the exciting coils.
Field Coils: Field coils are the coils of a conductor wounded across the pole core. When current is passed through these coils the poles react as an electromagnet and magnetic flux is produced in it.
Armature Core: The Armature core is cylindrical or drum-shaped and is built up of circular steel sheets or laminations. It is set to the shaft.
- Armature Winding: The armature windings are in a wound form. These windings are insulated from each other and normally copper winding is generally used in it.
- Commutator: The commutator provides a collection of currents from the armature winding or conductors. It converts the alternating current which is induced in the armature conductors into direct current (DC).
- Brush Gear: Brush gears holds heavy carbon brushes and are used to transfer huge amount of excitation current from it to the terminal junction.
- Capacitor: A capacitor is a basic component of a DC Generator which is used to remove some fluctuations and filter the DC output supply from its output terminals.
- Load Junction: The load junction of a DC generator consists of the two output terminal wires negative and positive which are installed in the terminal box to provide the load current and are used to connect the load supply on it.
- Terminals: In some modified DC Generators, the manufacturers provide an easy junction for the load and the manufacturers provide the two wires that are already connected to the load junction these two wires are assembled and installed in the main cover or yoke of the DC Generator to connect directly to the load connection.
- Suppressor Box: The Suppressor box is used to reduce the irrelevant and unwanted noise of a high KV-rated DC Generator.
- Terminal Cover: A terminal cover is a cap that protects the joints of the DC generator terminals and the load terminals and this cover is also used for safety measures to prevent electric shock and fire.
- Carbon Brushes: In a DC generator, Carbon brushes are used to collect current from the commutator and then transfer it to its main contacts.
- Bearings: Bearings are used to rotate the shaft very easily. Usually, ball bearings are frequently used in heavy machines due to their flexibility.
- Bearing Support Head: Bearing support head looks like the shape of the bearing and it holds the bearing in its case to provide support and alignment and it is fixed to straighten the bearing.
- Shaft: A Shaft of a DC Generator is a mechanical component. It consists of mild steel and it provides torque and rotation.
- Shaft Spline: A shaft spline is a small component installed on a shaft sometimes it is fixed on a shaft and sometimes it comes in variable form. A shaft spline consists of teeth and is in a circular form and is used for coupling/joining the other shaft to it for mechanical input for the DC Generator.
- Clamps: Clamps are used to hold the load wires tightly and make the load terminals safe and clean.
- Window Strap: The window strap is basically a net made up of iron and it is connected to the yoke it is used to provide an air gap to the DC Generator for the purpose of cooling.
- Retaining Cap: The retaining cap is made up of an alloy of non-magnetic steel and is tightened on the shaft to provide support to the shaft against centrifugal forces during rotation.
- End Cover: The end cover is a part of the yoke and it covers the end of the DC Generator with the help of bolts it is used to protect the generator from its end.
Yoke/Main Cover
The yoke is the main cover of the DC Generator made up of iron or any other material. It provides mechanical support for the poles. It acts as a protective cover for the whole machine. It also carries the magnetic flux produced by the poles. These yokes are made up of cast iron and for large machines cast steel or rolled steel is used.

Pole Cores
Pole Cores are used as field magnets. These are used to spread out the flux in
the air gap and it is also used to support the exciting coils. Pole cores are solid pieces and are made up of cast iron or cast steel. In the modern age pole cores are made up of thin laminations of enameled steel. The thickness of lamination is from 1 millimeter to 0.25 millimeter. The laminated poles are more secure than
the solid-piece pole cores.

Field Coils
Field coils are the coils of a conductor wounded across the pole core. When current is passed through these coils the poles react as an electromagnet and magnetic flux is produced in it.

Armature Core
The armature core is cylindrical or drum-shaped and is built up of circular steel sheets or laminations. It is set to the shaft. The slots are punched on its outer side. In small machines or motors, the armature slots are set directly to the shaft. These laminations are used for cooling purposes for the armature and to reduce the eddy current losses and voltage drops. The circular stampings or slots are cut out in one piece.

Armature Winding
The armature windings are in a wound form. These windings are insulated from each other and normally copper winding is generally used in it. These conductors or winding is placed in the armature slots which are lined with insulation.

Commutator
The commutator provides a collection of currents from the armature winding or conductors. It converts the alternating current which is induced in the armature conductors into direct current (DC). It is cylindrical shaped and has wedge-shaped segments. These segments are insulated from each other. The number of segments is equal to the number of armature coils. Each segment is connected to the armature conductor through a riser or strip. These segments have V-grooves to prevent centrifugal forces.

Brush Gear
Brush gears hold heavy carbon brushes and are used to transfer huge amounts of excitation current from it to the terminal junction. Normally these are used in Highly Rated DC Generators. The brush gear is used to change its position according to the requirement whether you want a small output current or either you want maximum current the most important use case of the brush gear is to adjust the carbon brushes in different directions to get maximum DC output from the DC Generator.
Capacitor
The capacitor is a basic component of the DC Generator which is used to remove some fluctuations and filters the DC output supply from its output terminals. It provides smoothness in output voltage and provides constant voltage.
Load Junction
The load junction of a dc generator consists of the two output terminal wires negative and positive which are installed in the terminal box to provide the load current and are used to connect the load supply on it. This junction is very strong and the two wires are connected to the commutator from which they take DC in it and then provide it on its junction for the load connection.
Terminals
In some modified DC Generators, the manufacturers provide an easy junction for the load and the manufacturers provide the two wires which are already connected to the load junction and these two wires are assembled and installed in the main cover or yoke of the DC Generator to connect directly to the load connection.
Suppressor Box
A Suppressor box is used to reduce the irrelevant and unwanted noise of a high KV-rated DC generator. This box consists of various valves and some other filters like holes, iron rings, resistive nets, etc. Which are used to reduce the noise from the generator.
Terminal Cover
The terminal cover is a cap that protects the joints of the DC generator terminals and the load terminals and this cover is also used for safety measures to prevent electric shock and fire.
Carbon Brushes and Bearings
In a DC generator, Carbon brushes are used to collect current from the commutator and then transfer it to its main contacts. These brushes are commonly made up of carbon and graphite. These brushes are rectangular-shaped. These brushes are mounted on the brush holders and the brush holder is mounted on a spindle. These brushes remain joined with the commutator by a spring. A flexible copper pigtail is mounted on the top of the carbon brushes which convey current from the brushes to the holder.

Bearings are used to rotate shafts very easily. Usually, ball bearings are frequently used in heavy machines due to their flexibility. Ball bearings work very efficiently in heavy machines. The balls and rollers of ball bearings are packed in hard oil.

Bearing Support HeadBearing support head looks like the shape of a bearing and it holds the bearing in its case to provide support and alignment it is fixed to straighten the bearing and it provides complete support in a required direction to provide uninterruptible function.
Shaft
A Shaft of a DC Generator is a mechanical component. It consists of mild steel and it provides torque and rotation. It is prototype and long and it is used for coupling in DC Generator to provide mechanical energy.
Shaft Spline
A shaft spline is a small component installed on a shaft sometimes it is fixed on a shaft and sometimes it comes in variable form. A shaft spline consists of teeth and is in a circular form and is used for coupling/joining the other shaft to it for mechanical input for the DC Generator.
Clamps
Clamps are used to hold the load wires tightly and make the load terminals safe and clean.
Window Strap
The window strap is basically a net made up of iron and it is connected to the yoke it is used to provide an air gap to the DC Generator for the purpose of cooling and it provides a better temperature for cooling.
Retaining Cap
The retaining cap is made up of an alloy of non-magnetic steel and is tightened on the shaft to provide support to the shaft against centrifugal forces during rotation.
End Cover
The end cover is a part of the yoke and it covers from the end of the DC Generator with the help of bolts and it is used to protect the generator from its end.
Winding Element and Conductor in Armature
There should be two types of windings enrolled on the armature of the dc generator. These two windings are either single-turn coils or multi-turn coils. A single-turn coil has two conductors and a multi-turn coil has so many conductors. The conductors are placed in the slots of the armature. The side of the coil is known as the winding element.

Pole pitch
Pole pitch is the distance between the two head-to-head poles in a dc generator and it is the division between the number of conductors of armature winding and poles of the DC generator. For example: if there are 60 conductors and 4 poles then 60/4 equals 15 and this 15 is the pole pitch.
Coil pitch
Coil pitch is the distance between the two sides of a coil. If the coil pitch and the pole pitch are equal to each other then the coil span will be 180 degrees and the coil sides will be arranged under opposite poles and maximum EMF will be produced in the coil sides then we will use the term that the winding is fully pitched.
Pitch of winding
It is the distance between the two turns of a conductor. The pitch of the winding is denoted by Y. The formula to find the pitch of winding is given below:
Y = Yb – Yf For Lap Winding
Y= Yb + Yf For Wave Winding
Here YB is the back pitch and YF is the front pitch which is defined below:
Front Pitch
It is the number of armature conductors covered by a coil on the front of an armature is called the front pitch. It is the distance between the first conductor of a coil and the second conductor of the next coil which are connected together at the end of the commutator. For example, element 8 is connected to element number 3 so the front pitch YF will be
8 – 3 = 5.
Back Pitch
It is the distance between the two conductors of a coil in the armature which are connected to each other on the back side of the armature. It is denoted by YB. For example, element 8 is connected to element 1 on the back side of the armature so the back pitch will be
8 – 1 = 7.
Resultant Pitch
It is the distance between the two coils wound on the armature. This distance starts from the starting point of the first coil and ends at the starting point of the other coil wounded in the armature. It is denoted by YR.
Commutator Pitch
It is the distance between the two conductors from where these two conductors are connected to the commutator bar/segment. It is denoted by YG.
Single Layer Winding
It is a coil that consists of a single conductor or a coil of single conductors wounded on the single armature slot.
Double Layer Winding
In this winding, a coil consists of a single conductor, and one side of each coil (first half) is placed on the armature slot where the other half of the coil is already placed on that slot. It means that every slot of the armature consists of the first half of two coils and so on. The upper half of the coils are placed in the odd-numbered slots of the armature whereas the lower half of the coils are placed on the even-numbered slots of the armature.
Lap Winding
In lap windings, the front pitch and the back pitch are equal to each other. Both pitches should be in an odd arrangement. By this an emf is increased and more energy is produced in the armature coils.

Wave Winding
Wave windings is a process of winding in armature in which we use only one conductor on the armature slots and we fill the armature slots with so many turns of a single conductor when the first slot of the armature is filled then we receive the first end of the conductor and the second end of that conductor and then placed these two conductors on the same segment of the commutator. In this winding, the segments of the commutator are equal to the number of coils.

Types of DC Generators
DC generators are classified into two different types which are described below:

Separately Excited DC Generators
As described in its name these DC Generators are those generators whose field magnets are excited/energized with a separate source of DC as shown in the figure below:

Self-Excited DC Generators
Self-excited dc generators are those generators whose field magnets are excited/energized by the dc generator’s own producing current. The flux is present in poles through residual magnetism so that a current is produced in it and it energizes the field magnets of the dc generator. These self-excited generators are further divided into three types which are described below:
Shunt Type DC Generators/Shunt Wound DC Generators
In these types of dc generators, the field winding is connected in parallel with the armature, and this field winding is connected to the supply as shown in the figure below:

Series Type DC Generator/Series Wound DC Generators
In this type of dc generator, the field winding is connected in series with the armature. It consists of a few turns of thick wire and carries a full load current. These generators are also called as special-purpose dc generators and are used as voltage boosters in many places.

Compound DC Generator/Compound Wound DC Generators
Compound dc generators are further divided into two types which are explained below:
Short Shunt Compound DC Generator
Short shunt compound dc generators are those generators in which the shunt field winding is connected in parallel with the armature and the series field winding is connected in series with the armature as shown in the figure below:

Long Shunt Compound DC Generator
Long shunt compound DC generators are those generators in which shunt field winding is connected in parallel connection with the armature and series field winding whereas the series field winding is connected in series with the armature of the DC generator.

EMF Equation of DC Generator
Let
Φ = flux per pole in weber
Z = total number of armature conductors
P = no of poles in a generator
A = no of parallel paths in an armature
N = rotation of armature in rpm
E = EMF induced in the armature
Then,
Losses in DC Generator
Every electrical machine which consumes an electric supply has many losses during its operation and so much electric power is wasted. In a dc generator, there are many kinds of losses that occur during their operation these losses are iron losses, hysteresis losses, eddy current losses, copper losses, etc. These losses are mentioned below:
Iron Losses/Core Loss
These losses occur due to the iron core and magnetic flux produced in field poles and these losses are called iron losses/core losses. Iron loss consists of two losses which are described below:
Hysteresis Loss
This loss occurs due to the changing magnetization of the armature core and this magnetization reverses the polarity which causes the opposite flux and this flux starts wasting.
Eddy Current Loss
Due to the rotation of the armature core, it also cuts the magnetic flux and EMF is induced in the body of the core. This current has a low value and this current is known as eddy current due to the wastage of eddy current so this is known as eddy current loss.
Copper Loss
Copper losses are not produced if we use standard conductor/conducting material in the winding but sometimes the material is not good for conduction and it takes so much power that current cannot flow easily through this conductor. So, these are called copper losses.
Mechanical Losses
These losses are friction losses at bearings and commutator and air friction loss in rotating armature.
Stray Losses
The addition of Magnetic losses and mechanical losses are known as stray losses.
Power Stages of DC Generator
There are many power stages of a DC Generator and these stages are shown below:

Efficiencies of DC Generator
The efficiencies of a dc generator are given below:
Mechanical Efficiency
Electrical Efficiency
Commercial/Overall Efficiency
Applications of DC Generator
There are so many applications of DC Generator and some of these applications are mentioned below:
- Separately excited DC generators are used as boosters in the process of electroplating and as a regulator etc.
- Compound DC generators are used as the power supply for welding machines.
- DC generators are also used to reduce the voltage drops in feeders.