
A simple flowchart can explain the chemical products derived from propylene. Polypropylene is derived by the catalysis process, each sequence is specified as propylene is treated with benzene to get cumene and it is reacted with air to get cumene hydroxide and finally acetone.
Propylene is treated with acid to get three compounds trimer, tetramer, and n-olefins. Trimer and Phenol produce Nonylphenol. The tetramer is reacted with Benzene to produce Dodecylbenzene and is used for Detergent manufacturing. Similarly, n-Olefins are reacted with Benzene to get Alkylbenzene to produce Detergents. Another reaction mechanism to produce Acrylonitrile is reacting Propylene with Oxygen and Ammonia or by us Nitric Oxide and a catalyst.
Propylene is reacted with chlorine to get allylchloride which is used for glycerol. By using Hypochlorous and acid Propylene is converted to Propylene oxide.
Propylene derivative petrochemicals:
Acrylonitrile == used in home furnishings, Apparel.
n-butanol == used in amino resins, solvents, glycol ethers, plasticizers, acrylates
propylene oxide == used for urethane polyols, ethers, amines, propylene glycol
polypropylene == extrusion, fibers and filaments, injection molding
isopropyl alcohol == cosmetics, pharmaceutical, process solvent, acetone

Types of Reactors used for chemical reactions and chemical process
Reactors are types of equipment used for carrying out some chemical reaction, they are broadly classified based on the application and involved in the energy, food, health dialysis categories, and much more. We know that the nuclear reactor is the heart of a nuclear plant in the same way, for biological chemical reactions which take place in the human body are organic living molecules act as a complex reactor. Observing nature when a raw material converts into another product, leads to conversion, which is done in a system with a boundary and separated from the surrounding; this system is called a reactor.
People who work in the chemical plant will be familiar with this equipment, but to know more about the reactors helps a lot in the shift work and in their carrier too.
Without much discussion let’s see the types of reactors used for chemical reactions.
The three basic classifications of chemical reactors are
1. Batch reactor (agitator and baffle design play an important role).
2. Continuous stirred tank reactor
3. Plug flow reactor
Based on heating and cooling reactors are named as
- Internal heat or cooled reactor
- External heat or cooled reactor
- Jacketed reactor
Most chemical reaction is carried out with a catalyst to improve the time and conversion of reaction. Based on this parameter the subclass of the reactor can be distributed as:

1. Fixed bed reactor
2. Multi-tubular reactor
3. Slurry reactor
4. Moving bed reactor
5. Fluidized bed reactor
6. Thin or shallow bed reactor
7. Dispersion reactor
8. Film reactor
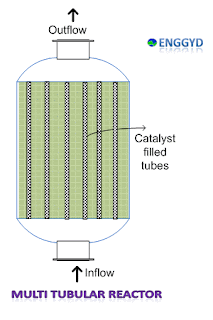
In design, a chemical reactor should have chemical reaction kinetic data and equipment design data with these in hand we can estimate the approximate design without wasting time, by following the below steps will lead to a sequence of the designing procedure.
1. Find out the product we need (its concentration, properties, and amount to be produced in a day).
2. Search some of the literature and patent information regarding the desired product reaction mechanism.
3. Does the process have side and undesired reactions?
4. The operating conditions like temperature and pressure required for the reaction to take place.
5. Go through the reaction kinetics and catalyst suitable to the reaction.
6. Now find out the material and energy balance of the whole process.
7. By using the various combinations of reactors and separation equipment draw the optimum flow sheet.
8. Include all the environmental and safety aspects with respect to chemicals and equipment.
9. Simulate the startup and shutdown of the plant designed.
You will notice some of the drawbacks in material balance and energy balance, by rectifying them you are ready with the design of the chemical reactor and chemical process which can be used for production.
Types of Pressure gauges
To measure absolute pressure, gauge pressure, vacuum or draft pressure, and differential pressure three physical methods can be used based on the working condition
- Using a liquid column where the density and height of liquid are important to measure pressure.
- Using pressure-sensing elements
- By electronic methods
Let’s see if pressure gauges of different types and pressure ranges can work.
Diaphragm Pressure Gauge:
This pressure gauge is widely used to measure the pressure of a reactor or closed container.
Principle:
When pressure is applied on either side of the tight diaphragm, by which it gets deflected. This deflection of the diaphragm is proportional to the differential pressure across it. Thus differential pressure across the diaphragm can be measured in terms of its deflection.
Construction and working:
Diaphragm gauge uses metallic or non-metallic diaphragms along with the pointer mechanism.
1) Metallic diaphragms: These elements are flexible circular discs, either flat or corrugated. These elements convert pressure signals to pointer deflection.
The metal is heat treated before forming a diaphragm to produce a maximum elastic limit. After forming, the diaphragms are heat treated to relieve internal stresses. A diaphragm is usually designed so that the deflections versus pressure characteristics are as linear as possible over a specified pressure range. Metals used are brass, beryllium copper, stainless steel, and phosphor-bronze.
2) Non-metallic diaphragms: very bendable diaphragms are used and so they can be utilized to measure vacuum and low pressures available. Non-metallic materials used are synthetic rubber, neoprene, leather, Teflon, nylon, or dacron.
Pressure range:
For non-metallic diaphragms 0 to a 10-inch water
Minimum= 0 to 2 inches of water
Maximum=0 to 400 psi
Advantages:
1. Small in size and cheaper
2. By using corrosion-resistant material it has a long life
3. We can obtain perfect linearity functions
Limitations:
1. Cannot be used for high pressure
2. Vibration will affect the reading
Related Topic